opportunities you might be interested in... 0
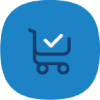
Mgr Global Supply Chain Performance & Improvement
We open up your world with every drive Would you like to work on the development of roof systems for future car models together with some of the market leaders in the automotive industry? Inalfa Roof Systems is a world leading supplier for OEM automotive roof systems and still growing strong. Are you ready to grow with us?The Senior Manager, Global Supply Chain Performance & Improvement, is a key member of the Global SCM team responsible for leading performance monitoring, improvements and risk management initiatives. This role contributes to strategic planning, standardization, and oversight, while supporting technology integration to enhance Inalfa global supply chain operations.The Global Supply Chain Performance & Improvement is a key member of the GL SCM team responsible for leading performance monitoring, improvements and risk management initiatives. This role contributes to strategic planning, standardization, and oversight, while supporting technology integration to enhance Inalfa global supply chain operations. Reports to: Sr. Director Global Supply Chain Management Your Main Tasks and Responsibilities Are: Performance Monitoring: Develop, Industrialize, rollout and analyze KPIs and dashboards to assess and improve supply chain efficiency.Data-driven improvements: together with regional organizations identify opportunities for continuous improvement and implement strategies and plans to enhance supply chain performance.Risk Management: Together with local and regional organizations identify, assess, and mitigate global risks / bottlenecks affecting the supply chain.Reporting: Prepare and present detailed reports based upon KPI driven supply chain performance and risk management to senior managementStrategic Planning: Contribute to the development and implementation of global supply chain strategies.Standardization: Contribute to definition of global aligned policies, standards and process documentation. Ensure uniform processes and standards across all regions. Document, validate and approve deviations. Enable and manage training structure accordingly.Oversight: Support gathering insights into new project quotations, oversee new product launches, track schedule and audit results related with Supply Chain.Technology Integration: Support the implementation of advanced technologies to enhance operations.Operational Support: Manage global capacity- and constraint management (Short- & Mid Term)Inventory Management: Develop/Improve the KPI Dashboard & manage the Inventory Workstream and awareness to the regions, developing improved management tools & highlights saving- and improvement opportunities. What Do We Expect from You: Education: Bachelor's degree in Supply Chain Management, Industrial Science, Business Administration, or related field; Master's degree preferred.Experience: Minimum of 8-10 years of experience in supply chain management, with a focus on operations, performance monitoring and risk management.Industry Knowledge: Proven track record in the automotive industry or other industries with complex and multi-tier supply chain operations.Technical Skills: Good level of understanding: ERP systems , IoT, and AI technologies.Analytical Skills: Strong analytical skills and proficiency in data analysis, visualization and reporting tools.What can you expect from us??13th month salary.Yearly valorization.III. pension pillar.Health weeks.Social program (company events, sports, culture etc.).Sick day.Our Core Values are?One Inalfa, Ownership, Ambition and Progress.?WE ARE IN IT TO WIN IT!Salary Range??2.678,00 - ??4.973,00Does this sound interesting to you? Don't hesitate and submit your application today.LocationKrakovany, Priemyseln?, 573/3Time TypeFull timeContact PersonBeena Nair


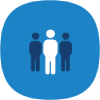
Team Lead- Workday
We open up your world with every drive Would you like to work on the development of roof systems for future car models together with some of the market leaders in the automotive industry? Inalfa Roof Systems is a world leading supplier for OEM automotive roof systems and still growing strong. Are you ready to grow with us? This position will be responsible for supporting global and regional HR teams with Workday. The Team Lead will pro-actively consult the business with new features and process improvements, driving towards a more HR Self-Service oriented operation. To ensure that all solutions are fit for purpose, you are able to gather requirements from HR, as well as advising them on best practices, options and implications. You will be reporting to the CHRO be based in Venray.Your Main Tasks and Responsibilities Are:Act as subject matter expert and pro-actively consult the businessManage changes and projects from start to finishStandardize and continuously improve the global Inalfa HR processes and dataAct as sparring partner for HR Operations to help them drive more toward global HR self-service technology and away from paper based, manual processesIdentify business needs by working with local and global teams, doing analysis, impact assessments and solution designProvide expertise on creating reports and configuring dashboards based on business needsProvide hands-on functional design and configuration (design, build, configure and test)Recommend on best practices and solutions based on the latest Workday featuresIdentify potential system issues and create plans and solutions to avoid or mitigate theseResolve incidents raised by key users in a timely manner What Do We Expect From You:Bachelor or Master Degree with solid working experience in an international organizationExtensive knowledge of Workday Core HCM, Recruiting and TalentGood understanding of Workday data and structure (including business processes, calculated fields, EIBs, security and reporting)As a professional, you have a service/customer oriented approach with good analytical and organizational skills. In your work, you focus on results and you are able to manage your planning and set prioritiesCollaborative work style and ability share knowledge with other team membersExcellent communication skills in English. Other languages are a plusWhat can you expect from us??Quarterly bonus.Holiday allowance.Free lunches.Medical care.Our Core Values are?One Inalfa, Ownership, Ambition and Progress.?WE ARE IN IT TO WIN IT!Does this sound interesting to you? Don't hesitate and submit your application today.LocationWrze?nia, Bia???yce 41ATime TypeFull timeContact PersonBeena Nair


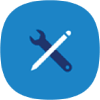
Project Engineer
We open up your world with every drive Would you like to work on the development of roof systems for future car models together with some of the market leaders in the automotive industry? Inalfa Roof Systems is a world leading supplier for OEM automotive roof systems and still growing strong. Are you ready to grow with us?Develop improved or new designs for automotive sunroof modules.Ensures that the product design meets customer and Inalfa Roof Systems specifications.Impact: Regional Typical Tasks, Responsibility:? ??Perform technical risk analysis using formal design engineering tools (DFMEA / GD&T / DFA / DFM / CAD / CAE / Design Reviews)??Perform feasibility studies based on technical specifications to create design concepts.??Perform basic technical calculations and design reviews to verify the proposed design.??Review and evaluate product designs concerning costs and manufacturability.??Utilize the CAD and PLM system, access and make minor updates to drawings. ??Support manufacturing and quality with root cause analysis for issues. ??Support Purchasing and SQD/SQE for technical issues of supplier. ??Perform cost reduction activities (VAVE) ??Local/global inter-company coordination and communication. Interface: Key member from Customer base & Project members from Inalfa & Supplier base. Functional Competence and Skill required: ?? Knowledge of product structure and manufacturing method for Auto parts. ?? Knowledge of engineering activities (FMEA, DOE, DFSS, GD&T, APQP, etc.) ?? Knowledge of databases relating to engineering documents and drawings. ?? Ability to use part, surface and assembly design and kinematics function in Catia. ?? Ability to work as a cross-functional team member. ?? Ability to work with customers as needed. ?? Ability to communicate with other regions in English. ?? Ability to use Microsoft Office (Specifically: Excel, Outlook, PowerPoint, and Word) ?? Strong problem-solving skills. Specific Requirements: ??Education: bachelor's degree or higher in Engineering. ??Experience and capability ? .Less than 5 years of automotive engineering experience. ? .Knowledge of the moving mechanism parts and manufacturing methods.What can you expect from us??Attractive working conditions and benefits.A culture focused on teamwork and solving problems together.An innovative atmosphere where new ideas are welcome!Opportunities for your personal and professional development.Our Core Values are?One Inalfa, Ownership, Ambition and Progress.?WE ARE IN IT TO WIN IT!Does this sound interesting to you? Don't hesitate and submit your application today.LocationHwaseong-si, Madogongdan-ro 2-gil, 39, MadoTime TypeFull timeContact PersonEunJin Lee ?????

