opportunities you might be interested in... 0
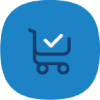
Mgr Global Supply Chain Performance & Improvement
We open up your world with every drive Would you like to work on the development of roof systems for future car models together with some of the market leaders in the automotive industry? Inalfa Roof Systems is a world leading supplier for OEM automotive roof systems and still growing strong. Are you ready to grow with us?The Senior Manager, Global Supply Chain Performance & Improvement, is a key member of the Global SCM team responsible for leading performance monitoring, improvements and risk management initiatives. This role contributes to strategic planning, standardization, and oversight, while supporting technology integration to enhance Inalfa global supply chain operations.The Global Supply Chain Performance & Improvement is a key member of the GL SCM team responsible for leading performance monitoring, improvements and risk management initiatives. This role contributes to strategic planning, standardization, and oversight, while supporting technology integration to enhance Inalfa global supply chain operations. Reports to: Sr. Director Global Supply Chain Management Your Main Tasks and Responsibilities Are: Performance Monitoring: Develop, Industrialize, rollout and analyze KPIs and dashboards to assess and improve supply chain efficiency.Data-driven improvements: together with regional organizations identify opportunities for continuous improvement and implement strategies and plans to enhance supply chain performance.Risk Management: Together with local and regional organizations identify, assess, and mitigate global risks / bottlenecks affecting the supply chain.Reporting: Prepare and present detailed reports based upon KPI driven supply chain performance and risk management to senior managementStrategic Planning: Contribute to the development and implementation of global supply chain strategies.Standardization: Contribute to definition of global aligned policies, standards and process documentation. Ensure uniform processes and standards across all regions. Document, validate and approve deviations. Enable and manage training structure accordingly.Oversight: Support gathering insights into new project quotations, oversee new product launches, track schedule and audit results related with Supply Chain.Technology Integration: Support the implementation of advanced technologies to enhance operations.Operational Support: Manage global capacity- and constraint management (Short- & Mid Term)Inventory Management: Develop/Improve the KPI Dashboard & manage the Inventory Workstream and awareness to the regions, developing improved management tools & highlights saving- and improvement opportunities. What Do We Expect from You: Education: Bachelor's degree in Supply Chain Management, Industrial Science, Business Administration, or related field; Master's degree preferred.Experience: Minimum of 8-10 years of experience in supply chain management, with a focus on operations, performance monitoring and risk management.Industry Knowledge: Proven track record in the automotive industry or other industries with complex and multi-tier supply chain operations.Technical Skills: Good level of understanding: ERP systems , IoT, and AI technologies.Analytical Skills: Strong analytical skills and proficiency in data analysis, visualization and reporting tools.What can you expect from us??13th month salary.Yearly valorization.III. pension pillar.Health weeks.Social program (company events, sports, culture etc.).Sick day.Our Core Values are?One Inalfa, Ownership, Ambition and Progress.?WE ARE IN IT TO WIN IT!Salary Range??2.678,00 - ??4.973,00Does this sound interesting to you? Don't hesitate and submit your application today.LocationKrakovany, Priemyseln?, 573/3Time TypeFull timeContact PersonBeena Nair


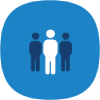
Team Lead- Workday
We open up your world with every drive Would you like to work on the development of roof systems for future car models together with some of the market leaders in the automotive industry? Inalfa Roof Systems is a world leading supplier for OEM automotive roof systems and still growing strong. Are you ready to grow with us? This position will be responsible for supporting global and regional HR teams with Workday. The Team Lead will pro-actively consult the business with new features and process improvements, driving towards a more HR Self-Service oriented operation. To ensure that all solutions are fit for purpose, you are able to gather requirements from HR, as well as advising them on best practices, options and implications. You will be reporting to the CHRO be based in Venray.Your Main Tasks and Responsibilities Are:Act as subject matter expert and pro-actively consult the businessManage changes and projects from start to finishStandardize and continuously improve the global Inalfa HR processes and dataAct as sparring partner for HR Operations to help them drive more toward global HR self-service technology and away from paper based, manual processesIdentify business needs by working with local and global teams, doing analysis, impact assessments and solution designProvide expertise on creating reports and configuring dashboards based on business needsProvide hands-on functional design and configuration (design, build, configure and test)Recommend on best practices and solutions based on the latest Workday featuresIdentify potential system issues and create plans and solutions to avoid or mitigate theseResolve incidents raised by key users in a timely manner What Do We Expect From You:Bachelor or Master Degree with solid working experience in an international organizationExtensive knowledge of Workday Core HCM, Recruiting and TalentGood understanding of Workday data and structure (including business processes, calculated fields, EIBs, security and reporting)As a professional, you have a service/customer oriented approach with good analytical and organizational skills. In your work, you focus on results and you are able to manage your planning and set prioritiesCollaborative work style and ability share knowledge with other team membersExcellent communication skills in English. Other languages are a plusWhat can you expect from us??Quarterly bonus.Holiday allowance.Free lunches.Medical care.Our Core Values are?One Inalfa, Ownership, Ambition and Progress.?WE ARE IN IT TO WIN IT!Does this sound interesting to you? Don't hesitate and submit your application today.LocationWrze?nia, Bia???yce 41ATime TypeFull timeContact PersonBeena Nair


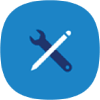
Manager, Manufacturing Engineering
We open up your world with every drive Would you like to work on the development of roof systems for future car models together with some of the market leaders in the automotive industry? Inalfa Roof Systems is a world leading supplier for OEM automotive roof systems and still growing strong. Are you ready to grow with us?Are you ready to shift into the next gear of your career? As a Manufacturing Engineering Manager you are in the driver's seat for driving the operations manufacturing engineering organizations towards the goal of excellence in the design, process, quality, cost reduction, facility, and equipment maintenance. This role plans, organizes, and controls all tasks associated with the accomplishment of all plant engineering objectives and measurable goals.ESSENTIAL DUTIES AND RESPONSIBILITIES include the following.?? Other duties may be assigned.Directs department activities to modify existing processes, improve production techniques and reduce cost.Supports manufacturing plant floor operations and the customer base by effectively managing all manufacturing engineering related issues.Resolve technical problems using solutions that involve new techniques, new technologies or concepts.Provides technical direction and leadership to engineering group for problem resolution and continued improvement of current operations performance.Ensures all manufacturing engineering activities and solutions meet or exceed engineering specifications, company standards, safety requirements and manufacturing requirements.Provides direction and examples for interpretation and application of company policies and procedures to all engineering activities.Plans engineering resources based on current / future projects, necessary production support and facility requirements.Maintains working knowledge of new technologies which may improve operations and develops recommendations accordinglyWork closely with Operations Quality, Product Engineering and SCM in coordinating all engineering change activities.Responsible for developing and tracking operating costs and managing the preparation of the departmental budget.Assist manufacturing personnel and advanced program team personnel by lending technical expertise during design and launch of all new programs.Responsible for training and personnel development plans for operations engineering group. All other tasks and duties as assigned by the General Manager. Manufacturing Engineering Manager, Operations Department, Inalfa Roof Systems, Inc.: Appointed as direct report to the General Manager. Direct, manage and control Inalfa Manufacturing Engineering Organization: Direct, manage and control all aspects of department activities to modify existing processes, improve production techniques and reduce product and process cost. Direct, manage and control all Inalfa Capital Equipment Expenditures for current production lines including expenditures of approximately $10 Million relating to tooling, fixtures, machines, equipment, and hand tools, to achieve timely acquisition for new vehicle roof systems assembly lines. Exercise complete control for department budget. Direct manufacturing engineering support of manufacturing plant floor operations. Manage resolution of technical problems using solutions that involve new techniques, new technologies or concepts. Provide technical direction and leadership to engineering group for problem resolution and continued improvement of current operations performance. Ensure all manufacturing engineering activities and solutions meet or exceed engineering specifications, company standards, safety requirements and manufacturing requirements. Provide direction and act as role model interpretation and application of company policies and procedures to all engineering activities. ?Plan and assure proper and timely implementation of all engineering resources based on current and future projects, and anticipated production support and facility requirements. ?Assure new technologies improve operations and develop recommendations accordingly to executive plant and operating management. Work closely with advance manufacturing, quality, product engineering and materials managers in coordinating all engineering change activities and to assure timely high-volume manufacture of new vehicle sunroof/body systems. Plan, develop and administer operating costs and preparation of departmental budgets. Evaluate subordinate personnel for career advancement and promotional opportunities within and outside of Manufacturing Engineering, Engineering and Operations organizations. Motivate subordinates to accomplish the tasks to satisfy and support the needs of the organization. Assure manufacturing engineering staff requirements for IATF16949 and QS9000 standards, and assure proper and accurate maintenance and updating of PFMEA, process documentation, environmental requirements and required action plans. Direct and control vehicle sunroof systems to solve customer complaints especially noise, water management and durability problems on current Inalfa programs. SUPERVISORY RESPONSIBILITIES The effective manufacturing engineering manager of operations shall motivate his/her team to accomplish the above tasks to satisfy and support the needs of the organization.? The continuing development of the engineering team is one of the most important position requirements. QS9000 RESPONSIBILITIES Follow manufacturing engineering staff requirements for IATF16949.? This includes but not limited to:? Update of PFMEA, process documentation, environmental requirements and required action plans. QUALIFICATIONS?? To perform this job successfully, an individual must be able to perform each essential duty satisfactorily.?? The requirements listed below are representative of the knowledge, skill, and/or ability required.??? Reasonable accommodations may be made to enable individuals with disabilities to perform the essential functions. EDUCATION AND/OR EXPERIENCE Bachelor?s degree in the technical field.? Additional experience related to sunroof technology and/or experience with mechanical / mechanism type components is preferred. LANGUAGE SKILLS (English) Ability to read, analyze, and interpret general business periodicals, professional journals, technical procedures, or governmental regulations.? Ability to write reports, business correspondence, and procedure manuals.? Ability to effectively present information and respond to questions from groups of managers, clients, customers, and the public. EXPERIENCE Minimum 3-5 years in tier one automotive supervising engineering activities is a plus.? Proven track record developing an effective technical team. COMMUNICATION: Must be able to communicate effectively with all levels of the organization. PHYSICAL DEMANDS The physical demands described here are representative of those that must be met by an employee to successfully perform the functions of this job. Reasonable accommodations may be made to enable individuals with disabilities to perform the essential functions. While performing the duties of this job, the employee is regularly required to walk and to sit; use hands to manipulate objects, tools, or controls; reach with hands and arms.? The employee is occasionally required to stand, stoop, kneel, crouch, or crawl; and to talk and hear.??? The employee must occasionally lift to 50 pounds.? Specific vision abilities include close vision, color vision, peripheral vision, depth perception and the ability to focus. WORK ENVIRONMENT?? The work environment characteristics described here are representative of those an employee encounters while performing the essential functions of this job. Reasonable accommodations may be made to enable individuals with disabilities to perform the essential functions. This employee works in an office and regularly works in the manufacturing area and is occasionally exposed to toxic or caustic chemicals.?? The noise level in the work environment is usually moderate. What can you expect from us??Paid vacation.Paid sick time.Healthcare, dental, prescription drug insurance plans.Company paid and voluntary life insurance plans.Disability benefits.Our Core Values are?One Inalfa, Ownership, Ambition and Progress.?WE ARE IN IT TO WIN IT!Does this sound interesting to you? Don't hesitate and submit your application today.LocationCherokee AssemblyTime TypeFull timeContact PersonJonathan Wyatt

